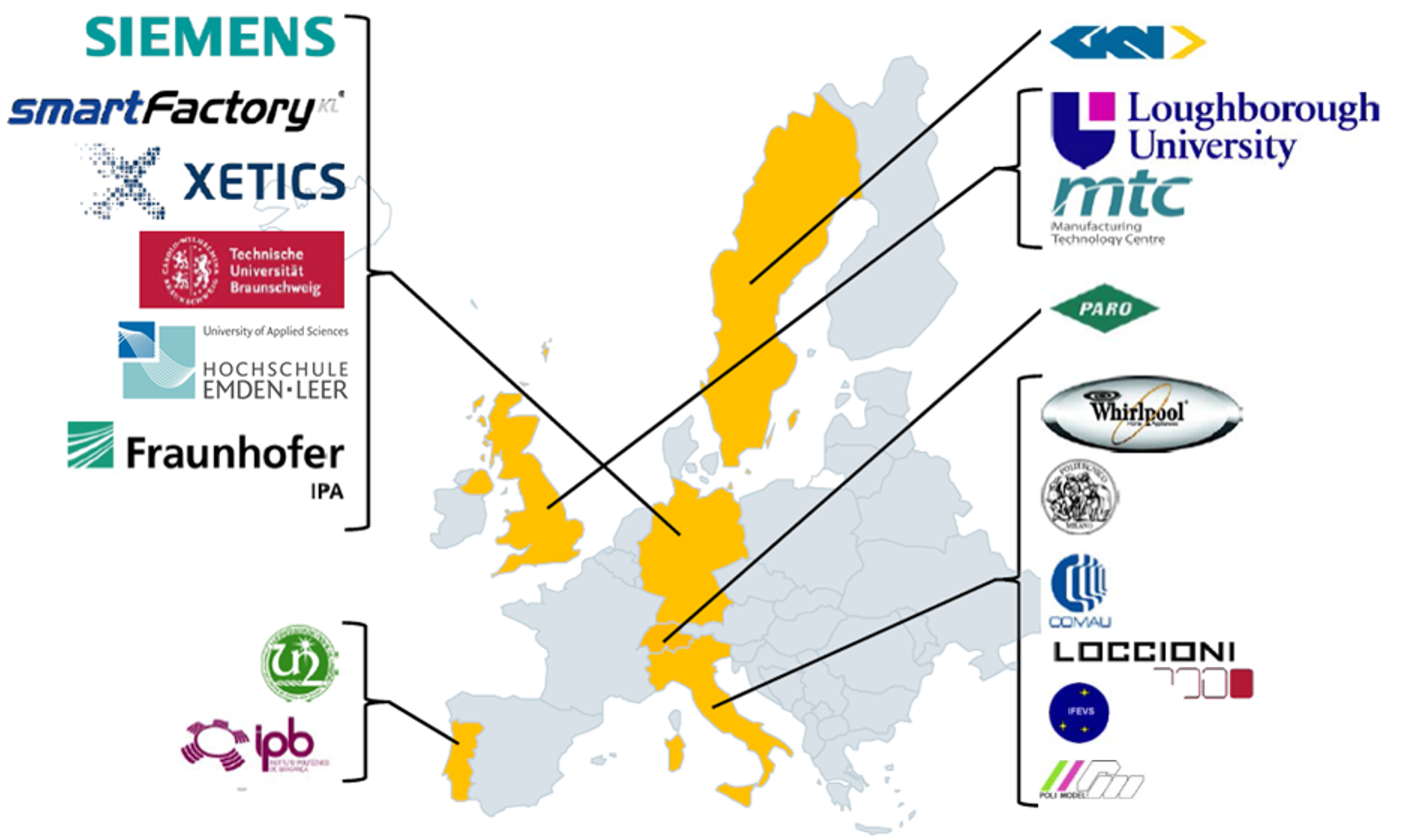
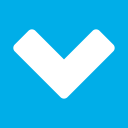

At the end of September 2014, Siemens had around 357,000 employees worldwide on the basis of continuing operations. More than 6,900 researchers and developers work at facilities in Europe, Asia and the United States for Corporate Technology (CT) to shape the technological present and future of Siemens, and help to better exploit its potential as an integrated technology company. As a reliable strategic partner to the Business Units, CT intends to make significant contributions along the company’s entire value chain, from research, development, production technology and manufacturing to testing. The regional presence is critical to understand local needs: CT's departments are a global network of specialized expertise that maintains a presence in important technology centers and global hot spots. As a single-source supplier and system integrator, Siemens combines all the expertise necessary for sustainable solutions in all areas of rail transportation. This leads to a balanced comprehensive approach to rail-based mobility from trams, light rail and metro services to commuter rail lines all the way to regional services.
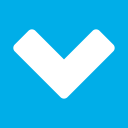
Whirlpool strongly believes in the power of brands and innovation to break out of an industry stalemate and challenge the market. Since 1989, Whirlpool Europe has invested more than 1.1 billion Euros in the development of its brands and the creation of innovative products that consumers are proud to own. This has proven to be a winning strategy and in just a few short years has allowed Whirlpool to become the number one brand in Europe (1996). Whirlpool invests in innovation as a key strength and distinguishing factor with regard to the competition, offering unique solutions that grant a competitive advantage and encourage consumers to choose Whirlpool products. Development at Whirlpool is driven by innovation at all stages, from design to the creation of new products, from marketing and sales strategies to supply and distribution processes.
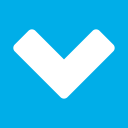

- new concepts,
- design and simulations,
- mass production of specific enabling systems (motor drives, transmission, HAVC, smart photovoltaic, remote control systems...),
- running vehicle prototypes,
- large scale production of Micro EVs.
- Micro EVs and M1 4WD and 4WS with two independent axles,
- Micro EV and first M1 having implemented battery partition with totally independent battery packs,
- Partial battery swapping concepts for advanced V2H.
- First microEV fully compliant with EuroNCAP most stringent safety ratings,
- Fundamental EMF rules to design a safe EV,
- Demonstrated 20km average daily range by smart photovoltaic only.
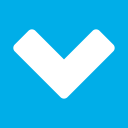
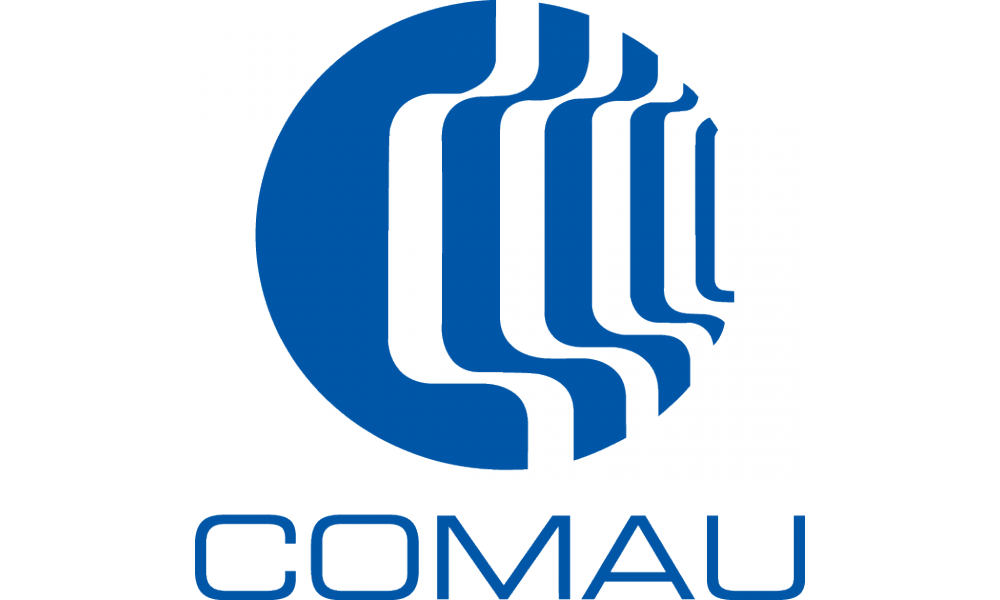
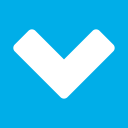
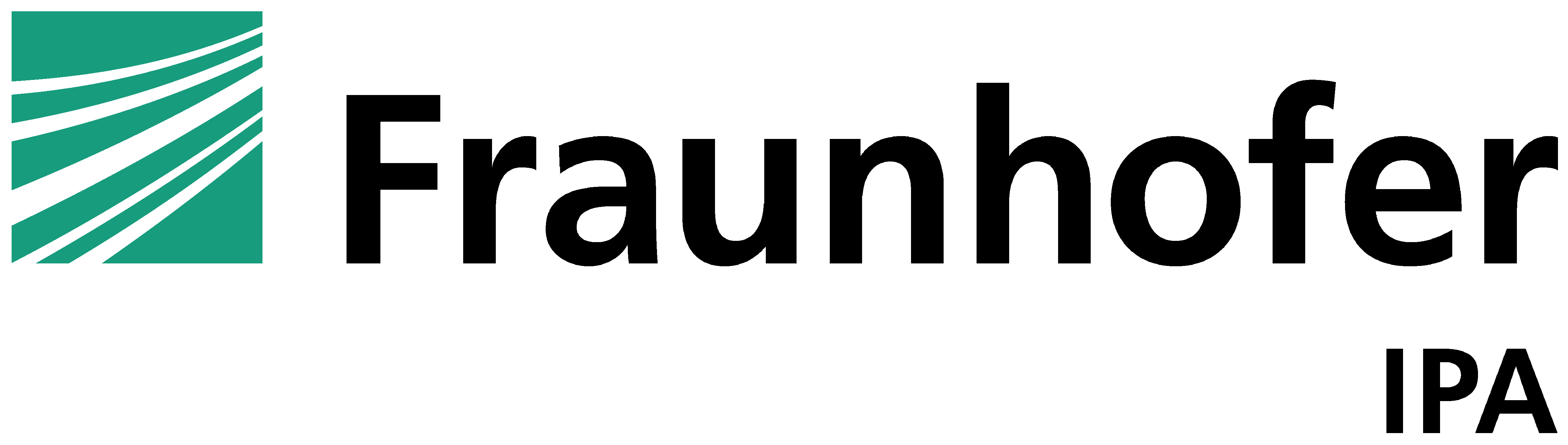
The institute disposes of know-how, many years of experience, human resources, fully equipped laboratories and technology – among others in the field of product design, process development, factory and production planning to factory operation and maintenance management by using innovative and state-of-the-art technologies and tools for modelling, simulation, visualization (VR) and optimization of products and factories. Additionally the Fraunhofer IPA expertise also covers software development and integration methodology, which is applied e.g. for equipment communication and integration, (intra)-logistics, simulation, scheduling, and evaluation of software and devices. It is actually participating to or leading a wide variety of European projects in regards to new manufacturing technologies, factory- and line planning, - simulation and -automation or production technologies. This also includes research related to the reconfiguration of manufacturing environments and flexible production systems as it has been executed e.g. in the XPress, FRAME, ManuCyte, or ManuCloud projects which have been funded by the European Commission. Based on these research activities, Fraunhofer IPA is also active in standardization. For example, it is a member of several IEC standardization consortia such as the TC65 WG 16 for digital factories, but also supports the IEC MSB (Marketing Strategy Board) with strategic recommendations. Furthermore, Fraunhofer IPA has contributed to the standardization roadmap for Industrie 4.0 and contributes to current discussions about standardization for CPS integration in manufacturing.
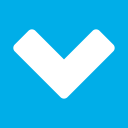
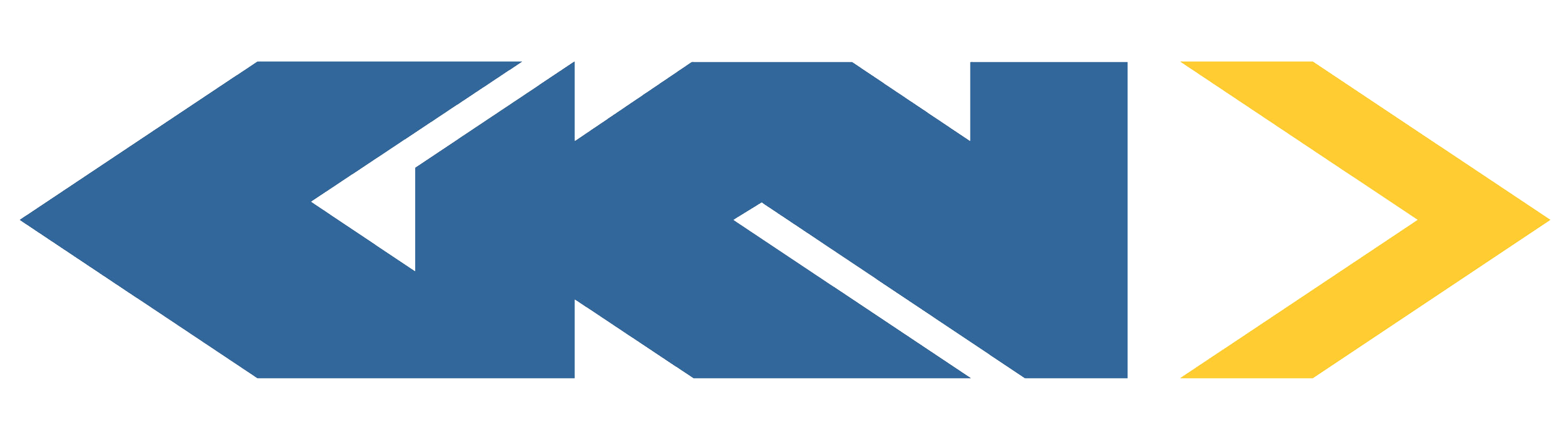
- Environmental care - GKN works actively to reduce the environmental impact in the design and engineering of tomorrow’s aviation engines.
- Technology - Make It Light; the lighter an aircraft engine is, the less fuel it consumes for any given flight. GKN focuses on developing lightweight solutions for aircraft engine structures and rotors, including a range of technologies developed through Swedish national programs and EU funded programs.
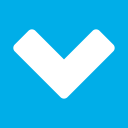
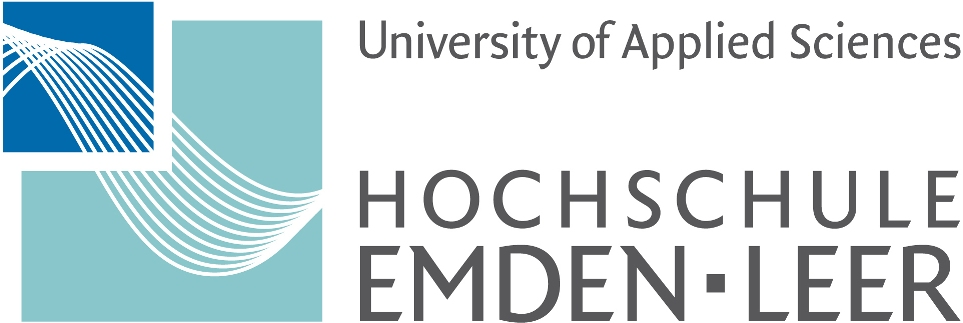
The research activities of the University of Applied Sciences Emden/Leer regarding engineering are endorsed by the institutes “Institut für Informatik, Automatisierungstechnik und Robotik” (I2AR), “Integrierte Produktionstechnik” (IP), “Lasertechnik Ostfriesland” (ILO), “Logistik” (HILOG), “Maschinen- und Anlagenbau” (MABU), “Medien und Technik” (IMUT) and “Energie- und Umwelttechnik” (EUTEC). Involved in the activities of the project will be mainly the institute I2AR, which has been founded in July 2001, is a non-profit research institute of the University with about 25 employees, mainly graduated engineers or working as Professors, as well as a number of students in practical training and master thesis students in the “Industrial Informatics” program. The main activities of I2AR aim at applied research in the field of Industrial Informatics Informatics. In particular, the research and innovation work concentrates on new ISA ́95-compliant platforms for the design, development, prototype implementation and corresponding validation of industrial smart cyber-physical systems using the Service-oriented Architectures (SoA), collaborative automation, cloud computing and multi-agent-based control paradigms as scientific and technological backbones. Here, the project will also benefit from I2AR ́s participation in system engineering groups within both German National and International scales, e.g. VDI/VDE, IEEE IES, OPC Foundation.
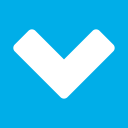
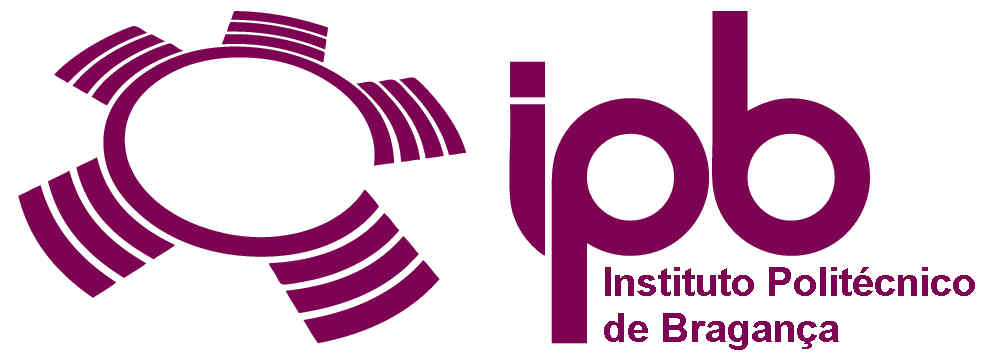
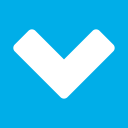
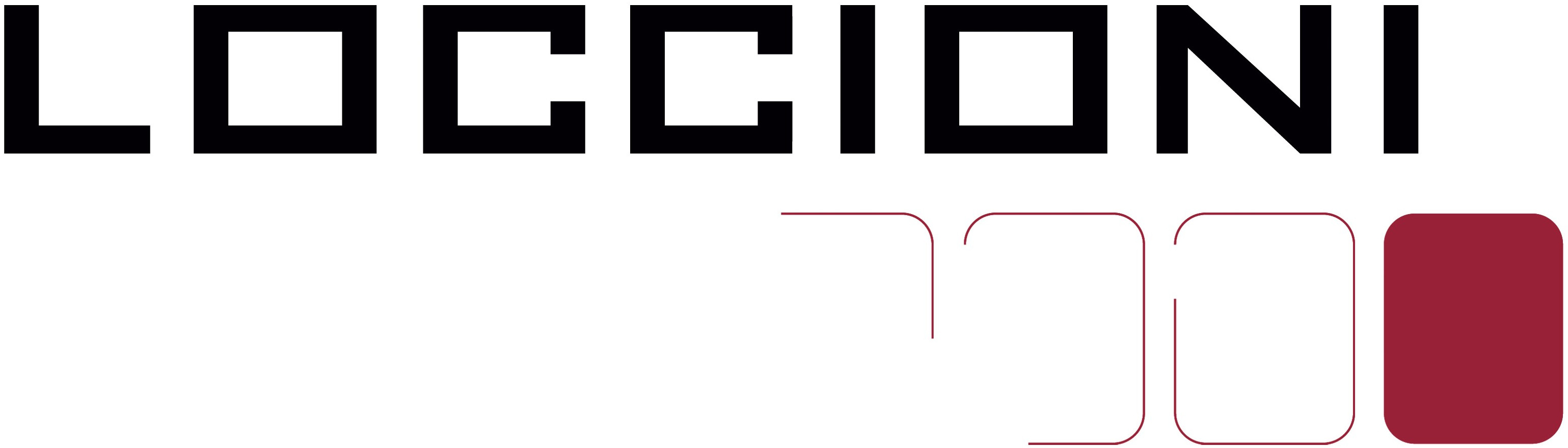
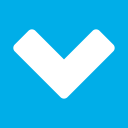
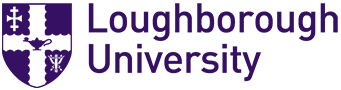
The EPSRC Centre for Innovative Manufacturing in Intelligent Automation is a partnership between Loughborough University, Cranfield University, Rolls-Royce, Air-bus, Aero Engine Controls, and the Manufacturing Technology Centre. The EPSRC Centre is part of a unique pipeline from discovery through to industrial deployment. Academics and researchers work collaboratively across the two sites and out with industrial partners, sharing their complementary expertise to develop truly multidisciplinary research. Resources include several large industrial robot arms, machine vision and motion sensing equipment. LU and the Centre have long standing expertise in successful management of large and medium sized research projects. The centre has a well-established professional management structure set up for to coordinate research programs with industry and national and international funding bodies. The centre will be supported by Loughborough University’s central research office with a proven track record for managing and supporting large research programs.
The centre is currently participating in 2 large EU FP7 research projects and co-ordinating 10 direct industrial research activities. In addition, the centre is driving knowledge transfer activities with local businesses and is responsible for outreach activities to engage local schools and colleges in STEM (science, technology, engineering and mathematics) activities in the area of intelligent automation. The centre has been involved in the development of new models for the design, ramp-up, operation and recovery of complex production systems and machines using latest knowledge modelling tools, collaborative design environments, semantic reasoning, sensor enabled intelligent plug and produce devices, industrial agents, and distributed diagnostics and prognostics models. As part of past and on-going project activities a number of semantic and probabilistic models have been developed to support the design, diagnosis, and validation of complex one-of-a-kind assembly systems using embedded intelligent devices. The accumulated expertise and know-how from these activities and developments is expected to be highly relevant for LU’s role within this project.
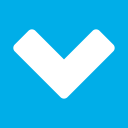
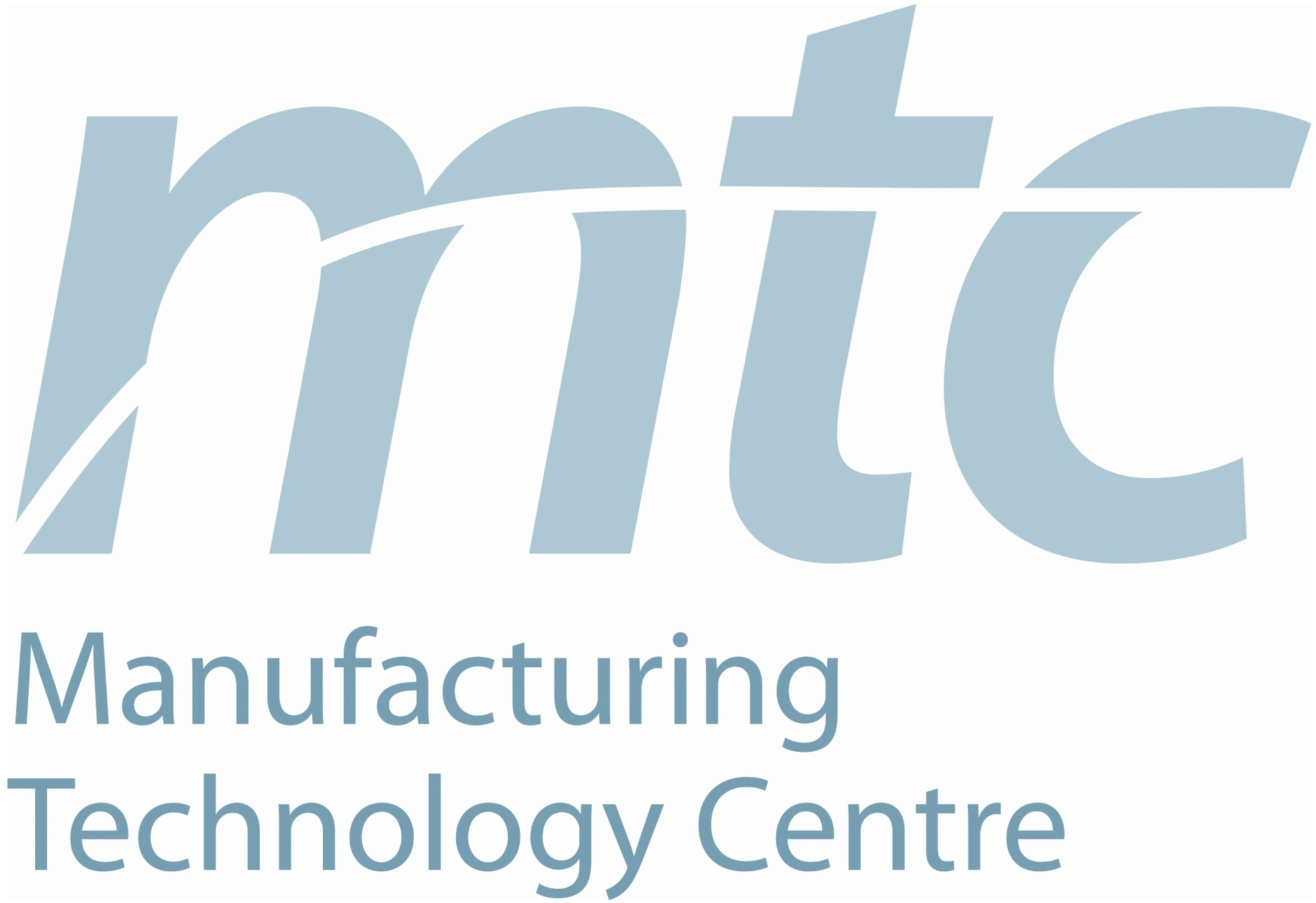
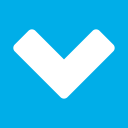
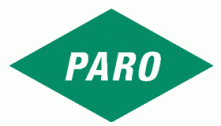
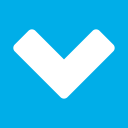
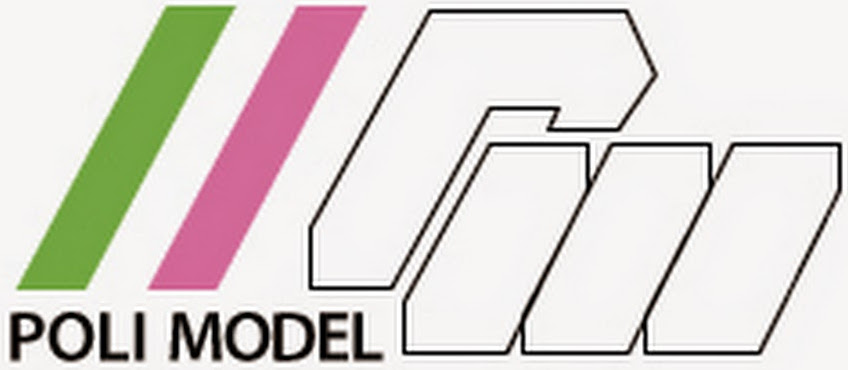
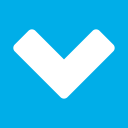
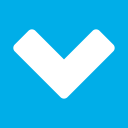
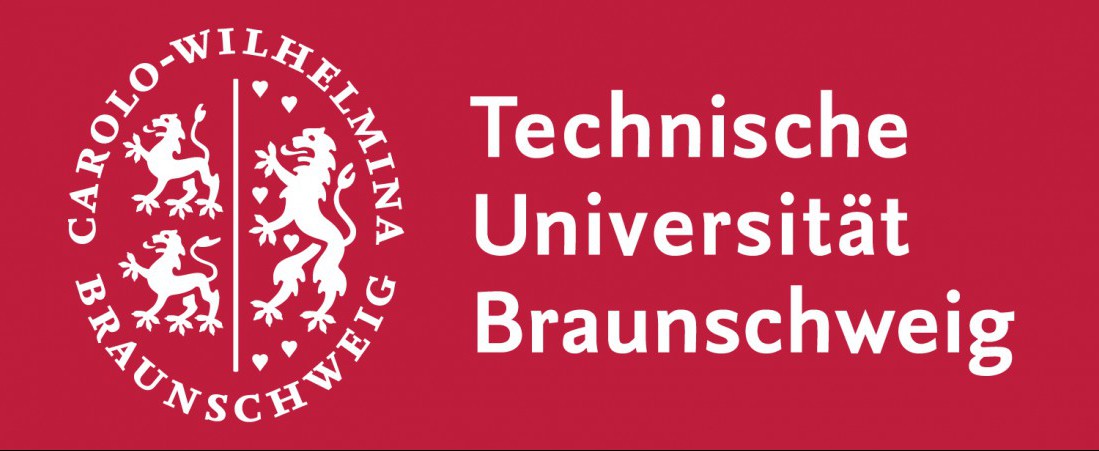
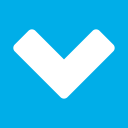

UNINOVA participated during the last few years in key EU projects that build the knowledge foundation to the work to be developed in the project. Of notice are the EUPASS-IP - Evolvable Ultra-Precision Assembly Systems, which was an important mark in intelligent modular assembly systems; the Self-Learning – Reliable Self-Learning Production Systems Based on Context Aware Services project studied how to build a service based production system highly adaptative and reconfigurable based on context learning; the InLife – Integrated Ambient Intelligence and Knowledge-Based Services (STREP) project developed services within several (operational) life-cycle phases: service to support installation and ramp up of lines, remote diagnostics and maintenance services during service-life, prevention of hazard situations, etc. to optimise operational costs and improve availability, reliability, and safety of assembly lines in these life-cycle phases; the IDEAS – Instantly Deployable Evolvable Assembly Systems project, which was flagged by the Commission as a success story, demonstrated a real industrial environment (FESTO) composed of agent based manufacturing modules proving concepts such as distributed control based on intelligent devices, evolution, adaptability, and self-organisation; the PRIME project is creating new solutions for deployment by SMEs of highly adaptive, reconfigurable self-aware plug and produce assembly systems, which will use multi- agent control, dynamic knowledge sharing, integrated monitoring, and innovative human-machine interaction mechanisms. UNINOVA aims to further extend its knowledge on multiagent based manufacturing architectures, while aiming at an extension of its RTD knowledge for future university curriculum, for future RTD projects as well as to transfer the envisaged projects results to industry, while also providing consultancy services.
UNINOVA is currently one of the top research institutions in designing and implementing service/agent based control systems for evolvable and adaptive complex production systems. The accumulated expertise and know-how from these activities and developments is expected to be highly relevant for UNINOVA’s role within PERFoRM project.
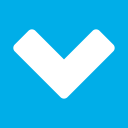
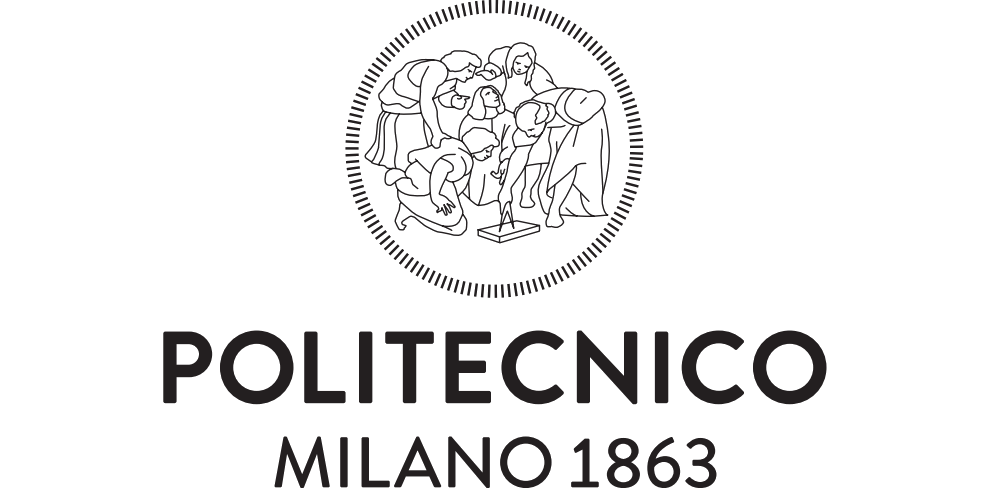
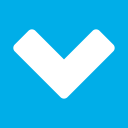

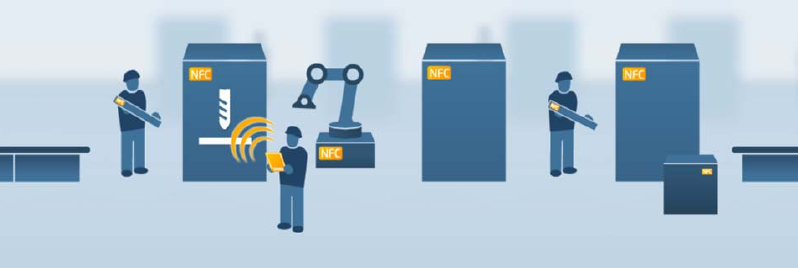
Deployment example with RF-ID (NFC) tags and mobile devices for light weight data acquisition From the IT-perspective XETICS customizes and adapts several IT-components and interfaces including the following:
- A cloud-based backend can be customized for data storage, aggregation and evaluation. This backend system can be adapted to integrate all other IT-systems. This will be done by providing interfaces for remote systems, like mobile devices, PLCs (i.e. via OPA, ...) or equipment using self-description and by integrating software components from other partners using libraries or a service architecture.
- A mobile (Android/iOS) App can be used for lightweight data-acquisition and support of maintenance tasks. Another important task which can be supported by mobile Apps is the monitoring of the health status to support real time decisions.
- A web-based User-Interface to the XETICS MES can be used to allow convenient access to the required information for production planers and equipment manufacturers. The provided web-based user interface is structured into several apps allowing the integration of software components of other project partners.