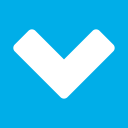
Project | Link |
IDEAS: | http://www.ideas-project.eu/ |
SOCRADES: | http://www.socrades.net/ |
GRACE: | http://grace-project.org/ |
IMS-AESOP: | http://www.imc-aesop.org/ |
PRIME: | Website has expired! |
To ensure the success of the project and the milestones of a new generation of agile manufacturing systems that respond dynamically, reconfigurable and viable to the ever-changing market, the project has a clear structure that includes 12 work packages. Each work package is divided into several tasks that result in one or more work package-specific results. The PERFoRM project contains six milestones marking the completion of key project-relevant phases (see Gant chart).
All work packages contribute to other work packages and identify the project unit leading to implementation in four use-case cases (see WP overview), represented by 18 partners from 6 different countries with excellent expertise in the various aerospace technology sectors, compressors, Household appliances and micro-electric vehicles The project PERFoRM is Michael Gepp, Partner SIEMENS, coordinates. The project started on 01.10.2015 and ends after a term of 36 months on 30.09.2018.
To ensure the success of the project and the milestones of a new generation of agile manufacturing systems that respond dynamically, reconfigurable and viable to the ever-changing market, the project has a clear structure that includes twelve work packages. Each work package is divided into several tasks that result in one or more work package-specific results. The PERFoRM project contains six milestones marking the completion of key project-relevant phases (see Gant chart).
All work packages contribute to other work packages and identify the project unit leading to implementation in four use-case cases (see WP overview), represented by 18 partners from 6 different countries with excellent expertise in the various aerospace technology sectors, compressors, Household appliances and micro-electric vehicles
The Work Package dependencies and the inherent agile / iterative development of the project can be seen in the Figure.
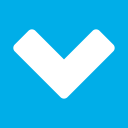
ICT has been the great enabler in the transformation of production systems from the classical centralized, monolithic and static organisation into an agile, highly reconfigurable, adaptable and dynamically interconnected to its external and internal environment – SMART FACTORY. Although Distributed Systems are already a reality in most shop floors, further actions are needed to fully exploit the benefits of fast reconfigurability, adaptability and rapid changeover. Hence there is a need to move in the direction of Cyber Physical Production Systems. The most noticeable features promoted by the CPPS paradigm are: development of plug-and-produce devices (self-contained equipment with dedicated individual control), acquisition of actual physical data by sensors that can be attached to the devices, usage of worldwide available data and services, communication technology, actuating the physical world by actors, and usage of multimodal interfaces.
The most important aspect in developing CPPS is the systems-of-systems aspect. In fact CPPS is composition of plug-and-produce devices, robots and machines (P an PR: plug-and-produce resource) that are plugged or unplugged according to the production system needs. The way these plug-and-produce devices are connected and interact with each other is one important research issue as it is how they are created, deployed and supported. Plug-and-produce devices have an identity, are able to communicate with each other and with the environment, configure and adjust themselves, store and deliver information in such a way that all together using their communication infrastructure define and create decentralized agile production systems. This communication infrastructure can also be used to plug a new set of services using the functions made available by the plug-and-produce devices and/or other services. Service composition is one fundamental aspect here as it will permit that new services are automatically or manually generated from the available ones.
With a large number of such interconnectable, standardised plug-and-produce devices it will be possible to create more agile factories provided a manufacturing service-bus created to allow their vertical integration into higher level business and production planning functions. This new company wide communication middleware must make plug-and-produce devices, robots and machines available to integrate them into the company wide operational control and business logic.
The concept of rapidly integrateable and self-adjusting plug-and-produce devices which can be combined with dynamic simulation, scheduling and optimisation methods to form agile production systems represents a radical new approach when compared to the traditional approach that can be found currently on shop floors. Previous projects such as IDEAS and SOCRADES proved the feasibility of distributed modular approaches at device level, while GRACE and IMS-AESOP proved that higher level services could be created based on a service or agent based approach, and PRIME is creating an industrial approach to create agent-based modular systems targeting in particular systems integrators. Therefore, it can be said that previous projects proved different individual solutions necessary to create an industry ready agile production system. However, none of them have proved the concept in an integrated form, which is necessary to achieve wider industrial uptake of these solutions. This is what PERFoRM aims to achieve. In addition to proving that these concepts can be seen in a holistic way, PERFoRM is aiming to harmonize these concepts and prepare standards to facilitate industrialisation and wider dissemination of plug-and-produce devices. Adaptors will be created for a range of devices, robots and machines to make them plug-and-produce ready by manufacturing service bus. In addition to providing a common interface for the plug-ability of production resources, the device adaptor will also allow more complex optimisation behaviour on local and global level. For example, an adaptor could facilitate the adjustment of robot trajectories when a new product is introduced or the repositioning of the robot (and its tool) for a better and more efficient execution of the task. This will be directly managed by the robot adaptor (based on the information received from the high level middleware) without the need for interventions by expert operators for re-programming the robot controller. With these adaptors, PERFoRM will ensure current devices and existing legacy equipment can be readily transformed into plug-and-produce resources.
With PERFoRM, true plug-and-produce devices are created by integrating existing TRL3-4 results and by following general concept of Cyber Physical Production Systems. Intelligent entities will be enabled to be plugged and unplugged into an industrial middleware. Common data and information interfaces and communication protocols for rapid integration and tuning will be prepared for standardisation. Adaptors for the integration of legacy resources will be created. In addition to this, vertical integration of plug-and-produce resources will be enabled to allow the creation of another level of services or applications that are attached to the enterprise network. These services and/or applications can compose data or information from the plug-and-produce devices (via the manufacturing service bus) and/or from other services. This way monitoring, simulation and optimisation methods can be deployed via the middleware and dynamically linked to the available plug-and-produce resources in the system. The middleware will be responsible to managing the connectivity when new resources become available or when they are removed. Also, the requirements of new products and their work flow through the system will be tracked by the middleware layer to allow higher level applications to focus on managing the production and business objectives rather than the updating of resource information. PERFoRM will specifically focus on integrating a multi-objective dynamic scheduling approach to manage work orders with flexible production systems. Ensuring consistent quality and reducing of energy consumption will be the main targets during the project.
The feedback form operators will be used to improve the changeover efficiency between different product variants.
This is expected to allow more frequent changeovers by ensuring quality targets can more easily be maintained (by
memorising past settings) or very quickly regained (by learning the most effective ramp-up and tuning strategies). The
combination of local self-adjustment mechanisms embedded into the device adaptors and the global dynamic
optimisation methods will allow existing and future manufacturing systems to become truly agile. The Figure illustrates the
core innovations of PERFoRM.
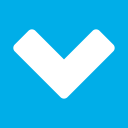
In this project, we really want to achieve a next generation of agile manufacturing systems that are dynamically
reconfigurable and evolvable to enable evolution, self-organisation and adaptation along the system life cycle, facing the
challenges of continuously and rapidly changing market conditions and increasingly smaller lot sizes and shorter leadtime
and time-to-market requirements. These systems should be based on modular plug-and-produce components (with
build-in intelligence) with all the different actors involved in the manufacturing system life cycle (module suppliers,
system integrators, end-users, …) brought together to smoothly design, deploy, ramp-up, operate, and reconfigure the
new generation of production systems.
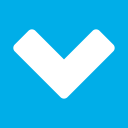
However, through simulation and four full industrial pilot applications it is PERFoRM intention to show and validate the
range of achievable improvements particularly for the performance indicators linked to productivity.
See the table below for an aggregation of the aspired project results, related impacts in terms of economic and
ecological KPIs with regard to the expectations laid down in the work programme and the related benefits for the partners and the European industry.
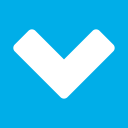
The first part of the work package will be a comprehensive study on existing integrated tools for the management of production systems, communication protocols and standards for data presentation with special focus on manufacturing and product data management models, communication and interoperability protocols.
The key performance indicators (KPI's) are defined below to reflect the impact on the industry and to be able to measure the social / ecological and economic aspect. These are defined for the entire project and in collaboration with the Work Packages 7-10 for each USE-CASE case.
Based on this information, the functional and non-functional requirements of the supporting information are developed technologies and tools defined. As well as the analysis for the best available technologies of the individual use cases. As a result, the guidelines for selecting suitable components based on features, implementation and integration characteristics, deployment efforts and availability specification defined by technical interfaces and supported standards.
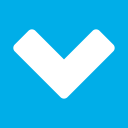
-
Workpackage objectives summary:
- Identification of the influence of humans as flexibility driver in production systems.
- Design the system architecture by harmonizing the research results from previous projects.
- Development of the industrial manufacturing middleware to support the communication and collaboration among the (hardware and software) production components.
- Development of the standard interfaces to support the plugability of (hardware and software) production components.
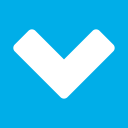
-
Workpackage objectives summary:
- Development of adaptors for interfacing, accessing, reconfiguring and controlling robots and other production resources
- Tools and methods to acquire and process real time data from production resources
- Support to decision making by the exploitation of real-time machine information at machine level
- Human expert support and integration at machine level
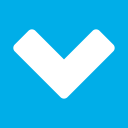
This work package contributes methods for the support of production planning. These are simulation methods for prediction, forecasting and visualization of plant relevant data to support the reconfiguration of the production system.
This work package aims to harmonize and prototype an appropriate simulation method to analyze the dynamic behavior of a production system. This method must be able to predict the performance of a production system regarding its energy and resource related key figures, production parameters and the integration of field device information. Furthermore, dynamic planning and (re)-scheduling procedures for job-shop production and flexible systems will be harmonized. An essential aspect in this context is the identification of critical internal and external success factors and drivers leading to guidelines and recommendations for implementation of agent-based production systems. Another objective deals with the adaptation of context sensitive visualization and monitoring tools for production data like machine parameters, energy consumption data and process parameters, providing quick assessment and decision support functionalities. The data ought to be processed user group specific and provided immediately, enabling rapid intervention and reaction to changes or disruptions within the production system on an operational level as well as for strategic decision making for production engineers and managers, e.g. as a dynamic dashboard. This work package also comprises recommendations for optimal reconfiguration mechanisms for machinery and robots to be used during the planning phase of new systems as well as for the improvement of existing ones including relevant aspects from the simulation and scheduling methods. The work package objectives also contain the harmonization and standardization of production system models coming from previous projects such as IDEAS and GRACE in an appropriate software environment.
-
Workpackage objectives summary:
- Harmonization of the multi-objective simulation method including energy-related aspects.
- Derivation of energy and agent-based dynamic planning and (re-)-scheduling procedures.
- Provision of optimal decision support and KPI and functionality visualization.
- Recommendations for optimal reconfiguration and modularization mechanisms for machinery and robots including respective boundaries.
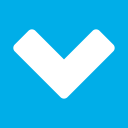
An integration and deployment process accompanied by a migration strategy needs to define what the migration is aiming towards, it´s justification what is the motivation and how it is influenced by the innovative control system strategy, like “best of breed” and/or consolidate on one system. This will also include how to isolate older-legacy systems and have them integrated, for the more modern innovative system, as far as possible, to act as if they would be one of those. At the same time the old-legacy system should see their surrounding systems as being of the same system generation. In this type of cases and from architectural and functional viewpoints, gateways, APIs and mediators play important roles.
From the business viewpoint, one of the main obstacles for broad implementation of new technologies within production environments is that they may put a high risk of loss of production if not fully tested. To mitigate these risks, WP 5 will deliver a detailed planning for the migration for the four use cases present within this project. For the integrated results from previous work packages, it will be defined which results need further testing and validation before they may be applied to the shop floor. This will be done together with the use case providers (e.g. factory leaders; engineers from factories). Subsequently these technologies will be tested within WP 6. Only after approval from use case leaders within WP 6, these results will be deployed at factory site.
To coordinate the migration progress for the project results in different kinds of production environments, there will be a centralized coordination of the migration progress within WP 5, thus avoiding harmonized results from diverging within different use cases again. This allows the overall validation of the successful migration of technologies not only within the four use cases, but also for some additional show cases within the test beds in WP 6.
-
Work package objectives summary:
- Integration and harmonization of results from WP 2, 3 and 4
- Identification of technologies to be further tested and validated within WP 6 before they can be applied within use cases
- Detailed planning of migration strategies and deployment of innovative production systems within the four use cases
- Centralized control of the migration progress towards innovative production systems across all use cases
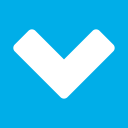
-
Work package objectives summary:
-
Verify and validate the technologies and methodologies developed in W2-5.
- Demonstrate the engineering feasibility and performance of a reconfigurable system in a relevant environment.
- Provide real data, information and knowledge to improve the technologies and methodologies developed in WP3-5.
- De-risk technologies and build a knowledge base to facilitate the implementation of industrial use cases in WP7-10.
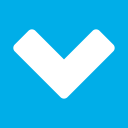
It is currently characterized by the production of one-of-a-kind-products or small lot sizes. The main production tasks are machining processes and assembly. A high share of manual labor and a high complexity in assembly results from the need of all components to be made available for assembling the final product.
The factory provides an ideal use case for the investigation of handling small lot sizes in an increasingly rapidly changing manufacturing environment with balancing costs, quality and customer demands at the same time.
One major goal is to achieve an increased availability of production equipment along the whole value chain (see picture), and especially in the early steps where individual parts are produced. Downstream from there along the value chain towards the final assembly of highly customized products.
More precise tracking and monitoring of parts and semi-finished products as well as monitoring of production equipment already was identified to be the first necessary steps to increase availability and streamlining the overall value-add process and gain better adaptability, more flexibility and increased resource efficiency.
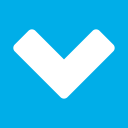
-
Specifically:
- Addressing quick adaptation of the production line from small lots of specific vehicles to larger lots of passenger cars.
- Minimizing human errors when selecting settings and parameters.
- Minimizing the variability of operations such as manual welding of the tubular chassis by introducing a high degree of robotized welding.
- Satisfying the highest automotive quality standards by tracking the incoming parts, sub-modules processes, and integration phases.
- Introducing testing methodologies on sub-modules before their integration.
- Introducing testing and quality evaluation methodologies on final products before delivery.
- Setting a data base for updates.
- Providing a safe, ergonomic and pleasant living environment.
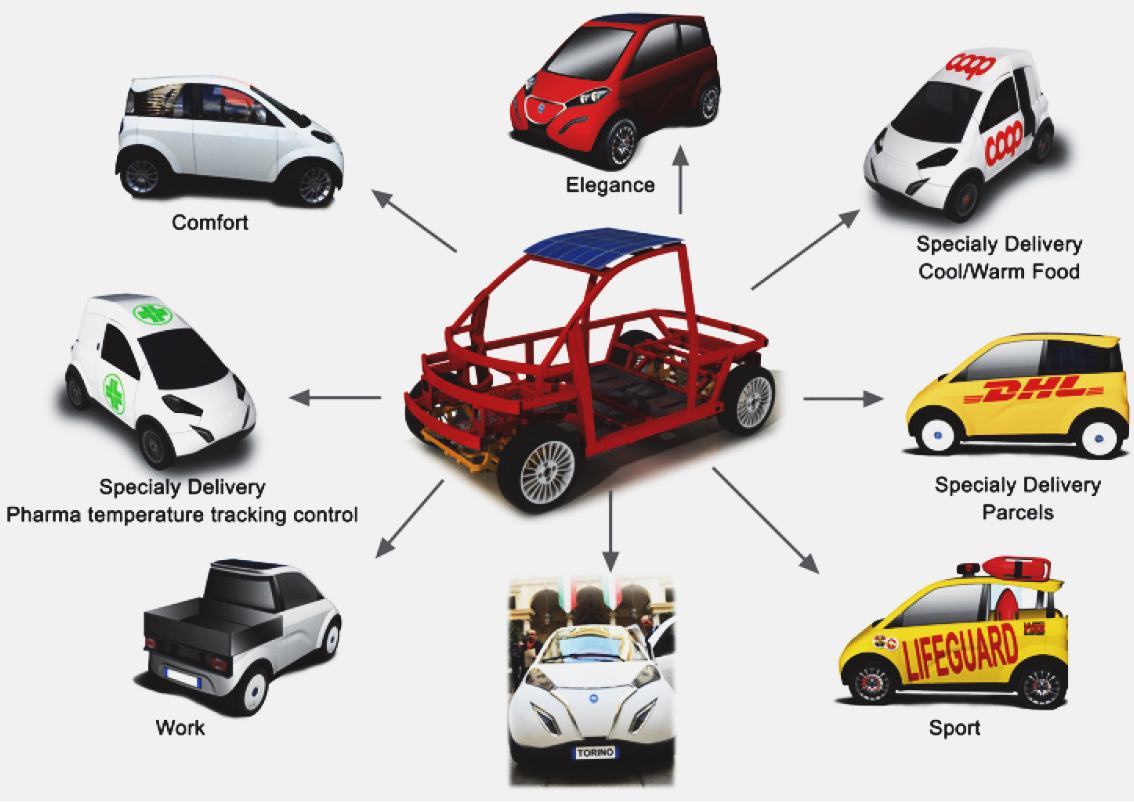
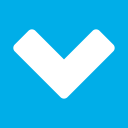
Whirlpool is one of Europe’s main producers of consumer white goods (e.g. refrigerator, ovens, cooktops, and washing machines) with a large variety in products and brands. To face the enormous pricing pressure in this market segment, continuous actions need to be undertaken to improve production. Within the production system implemented at Whirlpools sites, a Continuous Improvement Process (CIP) is established, which formalizes this process resulting in a one-year rolling plan. Clearly, in the case of highly agile markets (which white good definitive is) these plans help adapting and reconfiguring the factory to react quickly, and thus can generate significant competitive advantages. To ensure spending available (and strongly limited) capacity for improving measures in the most efficient way, deciding which measures to implement at what stage is a crucial step, and undertaking unnecessary action or solution with little impact needs to be avoided. Currently, these decisions are widely based on the knowledge and experience of involved employees. This does not always guarantee an efficient reconfiguration of production sites, especially as production equipment, challenges and personnel vary widely amongst different sites of Whirlpool and the amount of complexity each factory must deal with is increasing year over year due to the rate of differentiation of products and markets required by the globalized economy.
Therefore, in this use case a new kind of MES will be implemented with the focus to establish a “Reconfiguration Support System” (see picture), which continuously monitors the KPIs of a production environment and provides suggestions for reconfiguration of its components.
Based on those KPIs, creating the reconfiguration plan will be enriched and decision for undertaking specific actions will become more objective. After implementing appropriate measures, the impact of this on the factory KPIs will be easier recognized, generating high acceptance of CIM on a management and shop floor level.
-
Workpackage objectives summary:
- Conceptual design of “Reconfiguration Support System” to allow identifying measures for adaptation and improvement plan.
- Design and realization of hardware and software to implement “Reconfiguration Support System” based on a CPPS in an exemplary Whirlpool site or production line.
-
Testing and evaluation of the applicability of a “Reconfiguration Support System”.
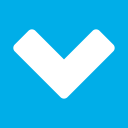
The “micro-flow” concept is designed to be a modular system with a large flexibility potential and be able to be adapted to different kinds of processes and products. The goal is also to make it a unit that can easily be moved to another location when needed. This will require integrated tools and solutions to facilitate fast reconfigurations and reduce time and cost for changeovers and moving from one location to another.
-
Workpackage objectives summary:
- Validate the CPPS concept and its functions for the demonstrator applications.
- Evaluate product processing flexibility, the lead time to introduce a new product variant.
- Evaluate process flexibility, the time to reconfigure the cell to another process application
-
Verify that risk mitigation is effective, and that traceability and product quality is not affected.
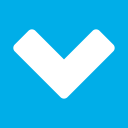
-
Work package objectives summary:
- Development and implementation of a business strategy for exploiting the project outcomes maximizing impact.
- Dissemination of project results to the scientific, technical and industrial audience.
- Contribution to related standardization activities.
- Establishment of a community to support PERFoRM innovation transfer.
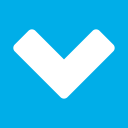
-
Work package objectives summary:
-
Monitoring, tracking and controlling deviations due to progress-, costs-, and scheduling- changes.
- Managing the project according to approved plans.
- Implementing procedures for quality management.
-
Implementing an administration and communication infrastructure to establish a basis for efficient and easy communication within the project, in addition to ensuring that external communication is done and controlled by the project management.
- Performing a procedure for updating and revising the plans every 12 months due to changes and new knowledge. All tasks will be accomplished by using state of the art management instruments and methods (see picture). This should facilitate an unobstructed and successful project and research evolution.
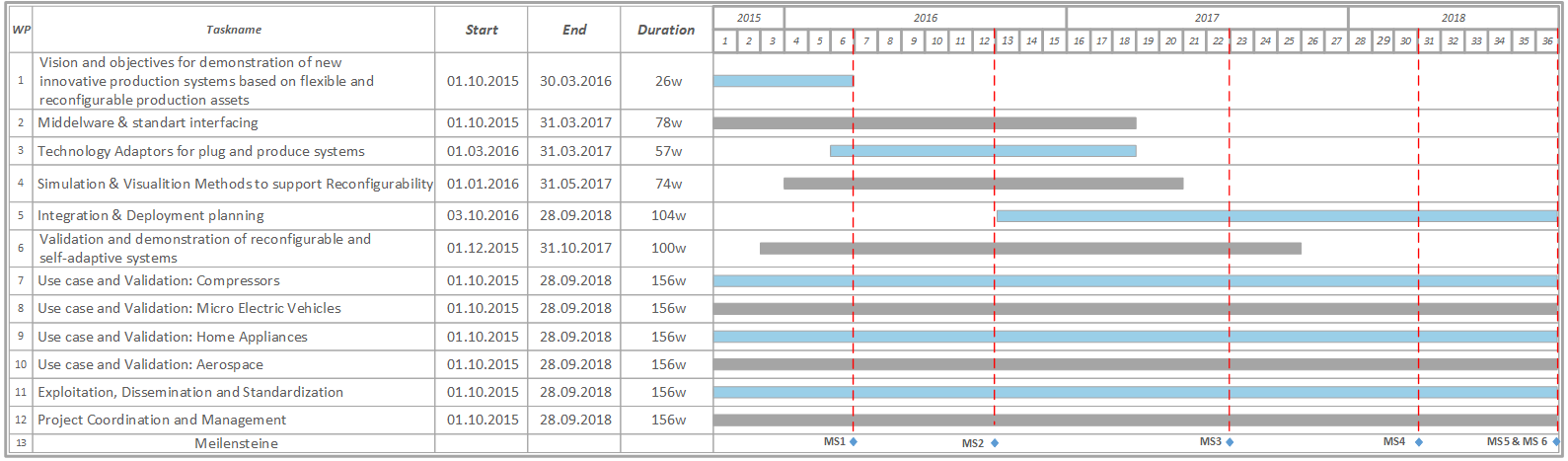